A Guide to Calibration Gases: Importance and Applications
Understanding Calibration Gases
Calibration gases are essential tools used in various industries to ensure the accuracy and precision of gas detection systems and analytical instruments. These gases are specific mixtures of one or more components that serve as a reference point for calibrating gas detectors, ensuring that measurements are reliable and consistent. The importance of calibration gases cannot be overstated, as they play a critical role in maintaining safety standards and operational efficiency across multiple sectors.
Industries such as oil and gas, mining, and environmental monitoring rely heavily on accurate gas detection systems to protect workers and the environment. Calibration gases help verify that these detection systems are functioning correctly, preventing potentially hazardous situations caused by faulty equipment. By using standard reference gases, companies can avoid costly errors and maintain compliance with regulatory requirements.
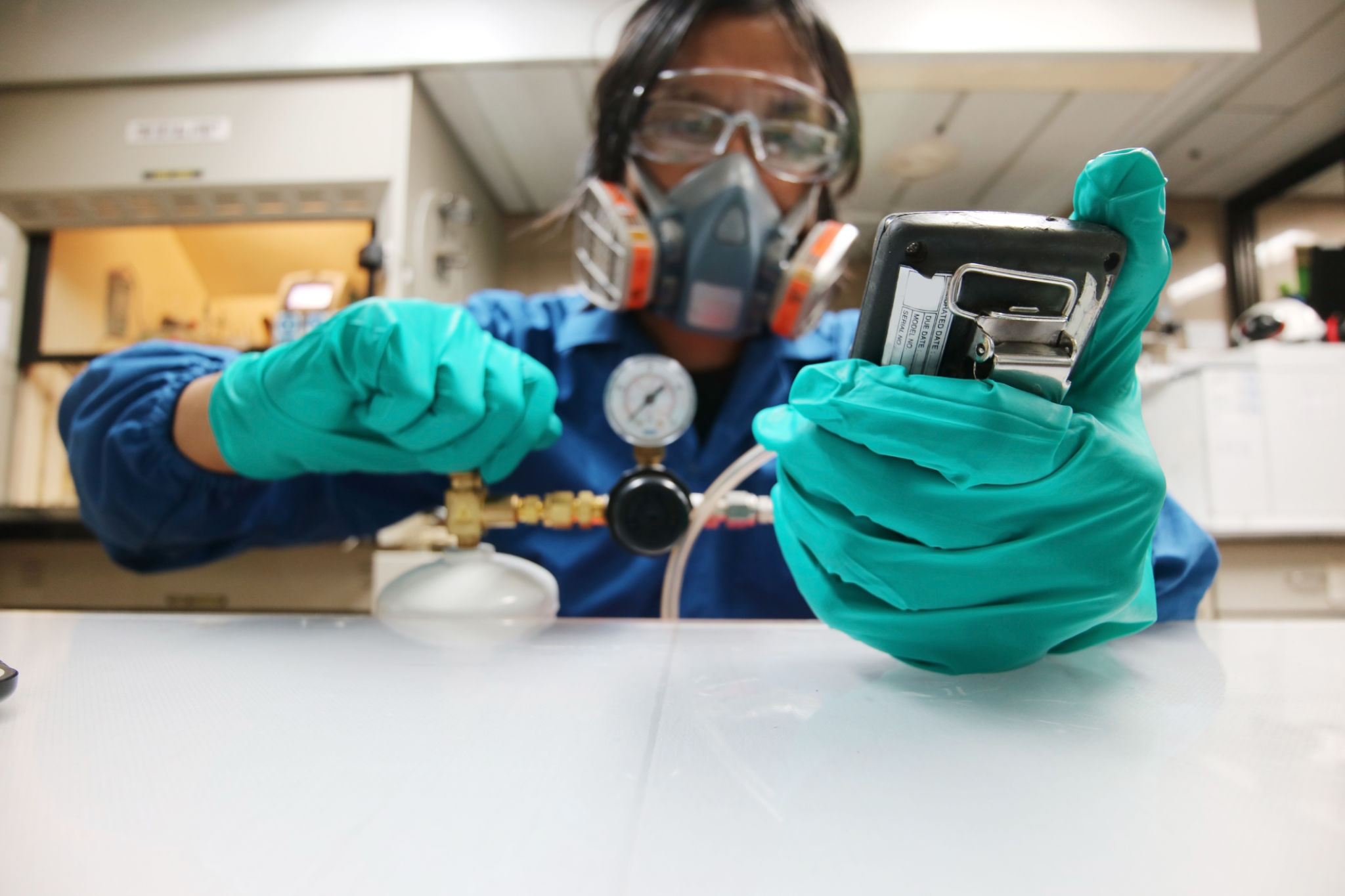
Types of Calibration Gases
Calibration gases come in various forms, each designed for specific applications. The most common types include:
- Single-component gases: These are pure gases used to calibrate detectors for a specific gas, such as carbon monoxide or hydrogen sulfide.
- Multi-component gas mixtures: These mixtures contain multiple gases, allowing for the calibration of detectors that measure several gas types simultaneously.
- Custom gas mixtures: Tailored to meet specific calibration needs, these mixtures can be customized according to the requirements of the instrument being calibrated.
The choice of calibration gas depends on the type of detector and the specific gases it is designed to measure. Selecting the appropriate calibration gas is crucial to ensure accurate readings and reliable performance.
Applications of Calibration Gases
Calibration gases are used in a wide range of applications. One of the most common uses is in the calibration of portable gas detectors, which are essential for monitoring potentially hazardous environments. These detectors are used by professionals working in confined spaces, industrial plants, and other high-risk areas to ensure safety and compliance with occupational health standards.
In addition to portable detectors, calibration gases are also used in fixed gas detection systems. These systems are installed in industrial facilities to continuously monitor air quality and alert personnel to any dangerous gas levels. Regular calibration with standard gases ensures that these systems operate effectively and provide accurate readings at all times.
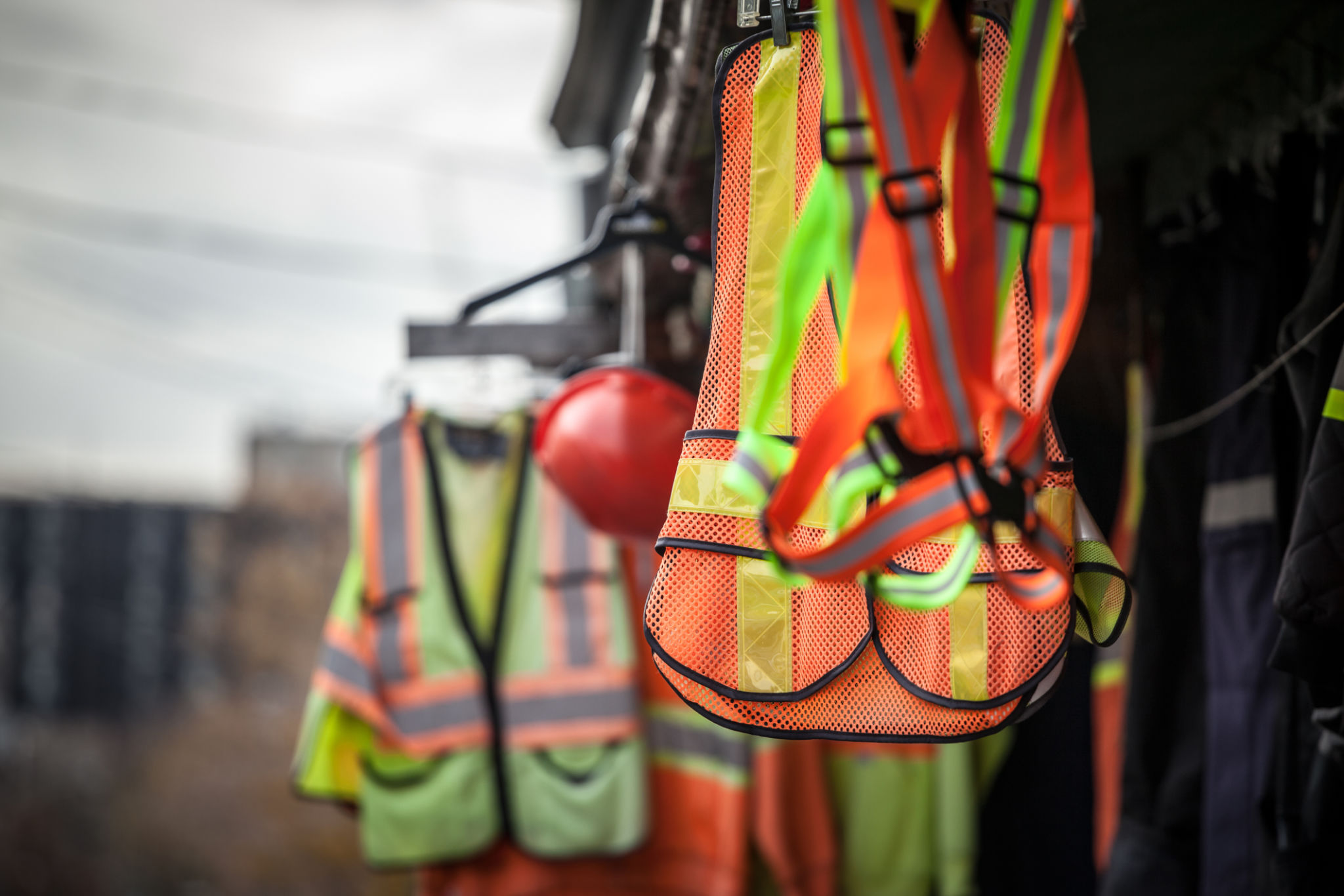
The Importance of Regular Calibration
Regular calibration of gas detection equipment is critical for maintaining safety standards and operational efficiency. Over time, sensors can drift or degrade, leading to inaccurate readings. By calibrating equipment regularly with accurate calibration gases, companies can ensure the reliability of their instrumentation and avoid potentially dangerous situations.
Furthermore, regular calibration helps extend the lifespan of gas detection equipment. By identifying and rectifying sensor drift early, companies can prevent unnecessary wear and tear on their devices, reducing maintenance costs and prolonging the life of their equipment.
Choosing the Right Calibration Gas Supplier
Selecting the right supplier for calibration gases is essential for ensuring accuracy and reliability. A reputable supplier will provide high-quality gases that meet industry standards and offer technical support to help companies choose the appropriate mixtures for their needs. It is important to verify that the supplier adheres to strict quality control measures and provides certification for their products.
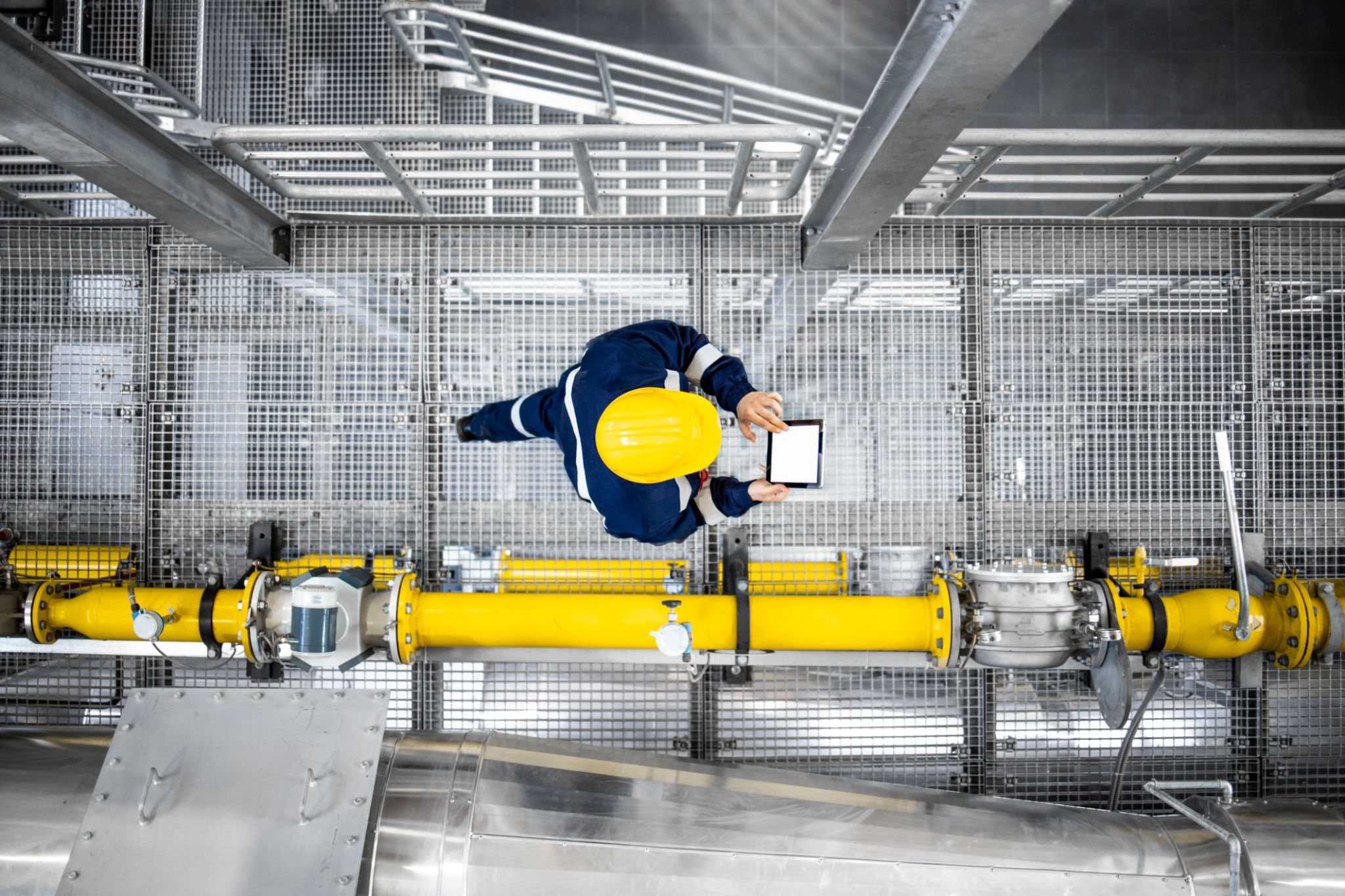
In conclusion, calibration gases are vital components in maintaining the accuracy and reliability of gas detection systems across various industries. By understanding their importance and applications, companies can ensure that their operations remain safe and compliant with industry standards. Regular calibration not only enhances safety but also optimizes performance and extends the lifespan of critical equipment.